Modular robot design
KUKA Roboter GmbH uses the EPLAN Engineering Center (EEC) for its electrical engineering design work; it provides its designers with a functional modular kit.
KUKA Roboter GmbH uses the EPLAN Engineering Center (EEC) for its electrical engineering design work; it provides its designers with a functional modular kit. The result is streamlined electrical engineering with an integrated data base that has been optimized for the modular system of the KUKA robot line. The "Art of Perfect Order", is reflected not only in the product, like palletizing robots, but also in the company's own processes. They palletize boxes and cartons, polish metal parts, sow leather seats, test operating components and weld car chassis: Robots have developed into universal helpers in all industrial environments. Approximately one million are being used worldwide. For the longest time the automobile industry was the main consumer, but nowadays there are specialized industrial robots for varying branches of industry, like for instance foundries, material handling and clean rooms. And they manage to infiltrate more and more fields of responsibility - e.g. as service robots or in the medical field. The robots are getting more flexible and more intelligent at the same time. For instance, they are able to literally work "hand in hand" with the operator. Or they are set up to cooperate, for instance with two heavy-duty lifting robots moving a car chassis along, and four other robots setting weld spots - this is a task that requires the highest degree of movement synchronization and therefore difficult steering engineering. Number one in industrial robots
The KUKA Roboter GmbH, with headquarters in Augsburg, is one of the market leaders in this exiting and demanding market worldwide; in Germany and Europe they even hold the number one position. The company offers a complete and broad product line of industrial robots and robotics systems, covering all standard load classes - starting with the mini robot, all the way through to the heavy-duty lifting robot, the "Titan", with 1000 kg load bearing capacity. The range of construction types is just as wide ranging. Some examples of the product line are the six axles robot, palletizing, portal-, clean room and stainless steel robot, heat resistant , SCARA- and welding robot. Modular construction allows flexible adjustments
Modular construction of the KUKA robots facilitates quick and simple changeovers for other tasks without any problems. All robots work with a tried and proven PC based steering platform - this innovation has brought KUKA into the world of robots in 1996 and thereby laid the foundation for mechatronic systems; they are the epitome of cooperation between software, steering and mechanics. Goal: Improved standardization and automation in electrical engineering
When the KUKA electrical design engineering performed the migration from EPLAN 5.70 to the new EPLAN Platform, to be exact to EPLAN Electric P8, the thought occurred to anchor a modular construction approach even more into the design methodology. Jürgen Albrecht, team leader of the electrical design department states: "Our entire robot product line is characterized by a uniform system philosophy, spanning across all technologies; the same operator units, as well as uniform maintenance and upgrade concepts. Meaning: The product line has already been streamlined and standardized on the electrical engineering level. This standardization on the product level opens up opportunities for a large degree of modularization and automation in the design systems as well." One such automation has already been done with KUKA on the basis of EPLAN 5.70. Electrical design engineer Gerhard Bauderer: "We have used the schematics generator from Eplan and created a link to SAP via CSV files. We could then activate the appropriate macros via SAP. But with time the generator began to offer an increasing number of modules so that there was a large degree of variation, and in the end standardization became rather difficult." Optimizing the processes by using the Engineering Center
The migration to the EPLAN Platform provided the perfect opportunity to tie in the new structures at this point. Jürgen Albrecht: "After we gathered all the information about our options with the EPLAN Engineering Center (EEC), we had made our decision: We wanted to use EEC for the optimization of the processes in the electrical design departments and benefit from greater flexibility, as well as the advantages of being able to work across projects.“ Designing with modular kits
In fact EEC really does have the best conditions for using these options. It facilitates the creation of modular kits based on functional modules, which the designer can then use to pick and choose for individual projects. In reality this looks something like this: he chooses a module, like for instance a linear axle, a gripper function, or a valve terminal, and enters the desired performance data or sizes. He then selects a mechatronic module from the modular kit, which already has the design data for all the trades involved, as well as the administrative data, like order numbers for instance. These modules are then compiled into a customer specific total solution and parameterized. Pesky side duties like for instance the selection of individual components from catalogs, listing specifications etc. are no longer necessary. And: All the data needed by the purchasing department and the in-house production are created automatically with the design. Careful planning: Which level should be selected for applying the modular concept?
Just as easy as the design is using EEC, just as thorough should be the preparations done ahead of time. Udo Dettmering, Electrical design engineer "The key question is: How should the module be structured? EPLAN has supported us extensively here." The future structure, after which the EEC would be modeled, was determined in a workshop: "One of the main objectives was to retain fexibility and openness for the future. Because to change the system afterwards would be too cost intensive. Therefore we had to give some thought to future structures in the fields of electrical and steering engineering. We looked at all of these together and came to the conclusion, that the best choice would be the smallest level for the modular kits, because of the high speed of innovations in our industry - this would help us stay flexible." High flexibility in spite of standardization
Gerhard Bauderer: "This structural principle does have the advantage that relatively few modules will be needed. It is sufficient now to call up the functions, to select the available modules, and to combine them into a plan". That is user friendly and very variable: "The system is so flexible that it actually could be used by our colleagues in the projecting business, who are developing individual system solutions based on our robots." The advantages of function based engineering
The KUKA electrical design engineers have used this approach to develop some first projects already. Gerhard Bauderer is completely convinced by this new engineering approach: "Working with the EEC modular kits is real and true progress for me. We save time, use uniform modules across products, and the plans, as well as the documentation are of considerably higher quality." Even constructing variants has become much easier: "We define a schematic for the basic design, containing as many options as possible, so that we need to build only a few variants - this has also been realized by using EEC." KUKA is currently in the process of programming the link to SAP. When this step has been completed, one can benefit from true integration in mechatronic engineering and is able to develop new, innovative products with standardized mechatronic function modules, and only a low investment in time.
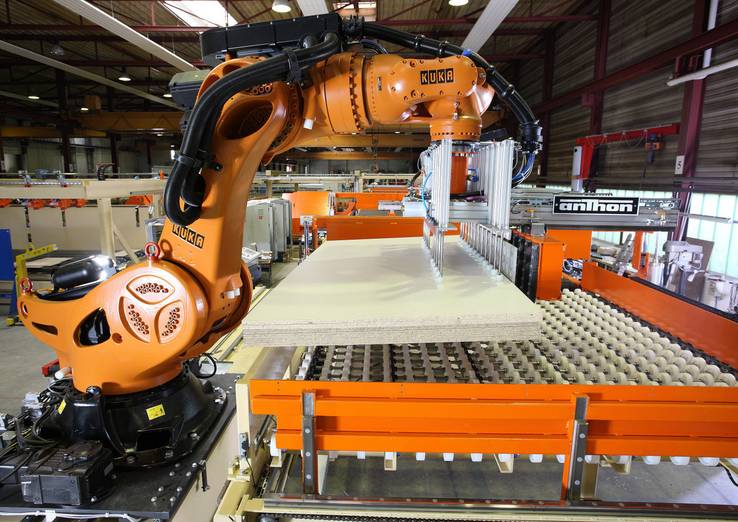
Kuka offers industrial robots and robotics systems, covering all customary load classes - starting with mini robots all the way through to the heavy-duty lifting robot, the "Titan", shown here, which can lift 1000 kg.

Jürgen Albrecht, team leader, electrical design engineering: This standardization on the product level opens up opportunities for a large degree of modularization and automation in the design systems as well."

Gerhard Bauderer, electrical design engineer states: "Working with the EEC modular kits is real and true progress for me". "We save time, use uniform modules across products, and the plans, as well as the documentation are of considerably higher quality."