The Wind of Change
SET from Austria is working on wind power generation using medium voltage synchronous generators powered by variable-speed variable motors via main drives and electromechanical differential gears.
The efficiency of wind power plants is measured based on the minimum achievable energy generation costs. Existing plants require large-scale, expensive performance electronics to synchronise the AC produced by the generator and coupled directly to the rotor with the network or large copper cross-sections for the high currents. SET from Austria is working on wind power generation using medium voltage synchronous generators powered by variable-speed variable motors via main drives and electromechanical differential gears. The consequence of the invention, which was made ready for market with solutions from EPLAN, among others, is a 5% increase in energy yield and power generation, even in light winds. With hub heights of up to 160 metres and rotor diameters of up to 150 metres, wind power plants are a clean, renewable energy source which can supply more than 5,000 houses with electricity per unit. They are mostly operated in large groups known as wind parks. Like photovoltaic systems, they are exposed to changeable natural forces and supply electricity with less regularity than traditional generation methods. One of the pioneers in the wind power sector is Dipl.-Ing Gerald Hehenberger. His career is characterised by the desire for increased system efficiency. He developed adjustable angle rotor blade powered systems with variable speeds and performance of 600 kW in the eighties, and followed up ten years later with dual-feed three-phased induction generators. This is the principle that around two thirds of all wind power plants work on today. Hehenberger then went on to found SET Sustainable Energy Technologies GmbH in Klagenfurt in 2008 in order to extract even more power from the same amount of wind based on a completely new concept. In order to achieve high yields even from low winds, wind turbines need to be able to convert variable rotor speeds into a constant generator rotation," explains Ing. Mag. Christoph Pilgram, Director of Business Development & Sales at SET. “One very good concept is differential gears with variable conversion ratios.” These have been in existence since the 1980s. However, they work on a hydraulic basis and therefore exhibit high levels of power dissipation which needs to be extracted in the form of heat. Electromechanics as the success factor Hehenberger's alternative idea, which the technicians at SET are currently developing to market readiness, is an electromechanical differential system. It consists of a planetary gear system where the input shaft is connected to the planetary wheels. The hollow wheel is connected to the medium voltage induction generator. A highly dynamic servo drive with approximately 15% of the nominal generator power is connected to the solar wheel and governs the gear behaviour thus allowing any fluctuations in speed to be balanced out. At the same time, the server has a torque control system which influences the effective power of the generator so that it can react directly to fluctuations in performance. The differential gear generator combination DSgen-set® achieves an overall efficiency of 97.5%. This is an unprecedented level and, by increasing energy yield by 3 to 5 percent compared to traditional variable-speed drive train systems, it can make a significant contribution to improving productivity. The system incorporated into the pod is also smaller and lighter because large elements of the failure-prone performance electronics are no longer required. At the same time, the direct generation of the energy at medium voltage saves on the step-up transformer in the wind power system and 70% of the copper cross section to it. "The high yield can be attributed to the fact that at the rated load, the servo drive also works as a generator and feeds power into the net. If the wind is very weak, the main generator is disconnected from the net, the system blocked by means of a differential lock and the servo drive is operated as a small, low-loss generator/full converter system," explains Christoph Pilgram. "So we can utilise even the lightest breath of wind." Mechatronic development The development of the servo controlled gear system and the associated synchronous generator, work on which began in 2009, is a project which combines mechanical design, electrical planning, instrumentation, and control technology. The electrical engineering element of the plants is developed using database-assisted EPLAN Electric P8. Based on a sophisticated platform technology, it gives the option of working in a graphic or object-oriented way. This, and the direct connection to the EI&C technology, provides very extensive, virtually unlimited options in terms of configuration, documentation and management of projects and supports interdisciplinary work. Data from previous planning phases can also be easily adopted via interfaces such as ODBC, XML and Excel. "We are benefitting from the option of incorporating finished data from upstream suppliers into the system," explains Ing. Michael Kofler, responsible for electrical engineering at SET. "By managing the shared database, product data maintenance can be carried out from any workplace but only needs to be done once." 3D design & construction SET opted for the AutoCAD Design Suite for the design of the mechanical parts at the beginning of the development process. "This guarantees quick, safe generation of documentation without taking up the creative energies of our developers," explains Christoph Pilgram. "At the same time, it promotes the exchange of ideas among the individual technicians and provides 3D concepts for experiments." So the bundle based on the current version of AutoCAD enables quick creation and high-quality output as illustrations based on the SketchBook Designer software can be incorporated. For the presentation of concepts as the basis for strategic decisions, the AutoCAD data can be quickly converted into 3D presentations in Software Showcase and made available for shared use online. Existing concepts and sketches in the form of paper documents and raster graphics can be converted into AutoCAD files using the Raster Design programme and then fed into the development process. The Mudbox software can be used to add colour and texture to the models to make them convincingly realistic. Alias Design creates production-quality surfaces. The software 3ds Max Design can then be used to convert the AutoCAD files into top quality 3D renderings. Knowledge stored in Autodesk Vault In order to meet the requirements in terms of data management, SET has worked with EPLAN Software & Service to develop a concept to allow efficient organisation, management and tracking of design data throughout the entire product life cycle based on Autodesk Vault. "In our development processes, it is not unusual for basic decisions to be made even during development," explains Dipl.-Ing Markus Waldner, Director of Control Engineering at SET, where this PLM tool can show off all its strengths. "It is particularly important to be able to trace all versions of the system step by step and be sure that the most up-to-date data is being used, with all additional information always on hand without time-consuming searching." Since 2012, additional information of all kinds has been stored in Vault alongside the design data in order to preserve the knowledge. The combination of EPLAN, Autodesk-Solutions including Vault has given SET a considerable advantage in the product development process.
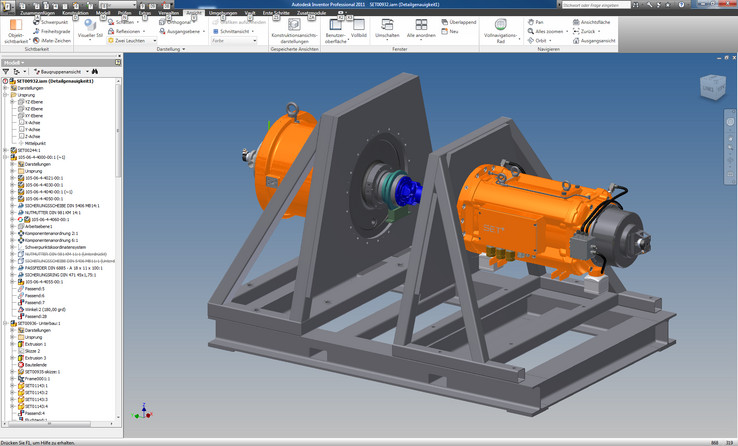
The generators and servo machines are designed in-house using Autodesk Inventor and are first produced as virtual 3D model prototypes.
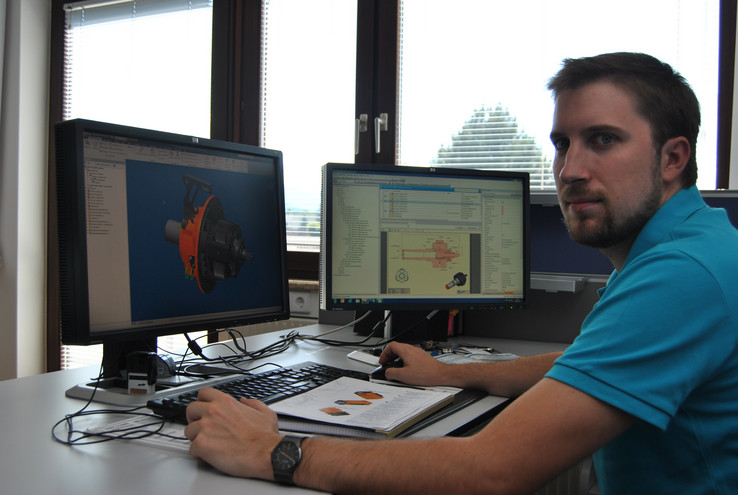
The mechanical design of the generators uses Autodesk Inventor within the AutoCAD Design Suite, likewise for the test bed.